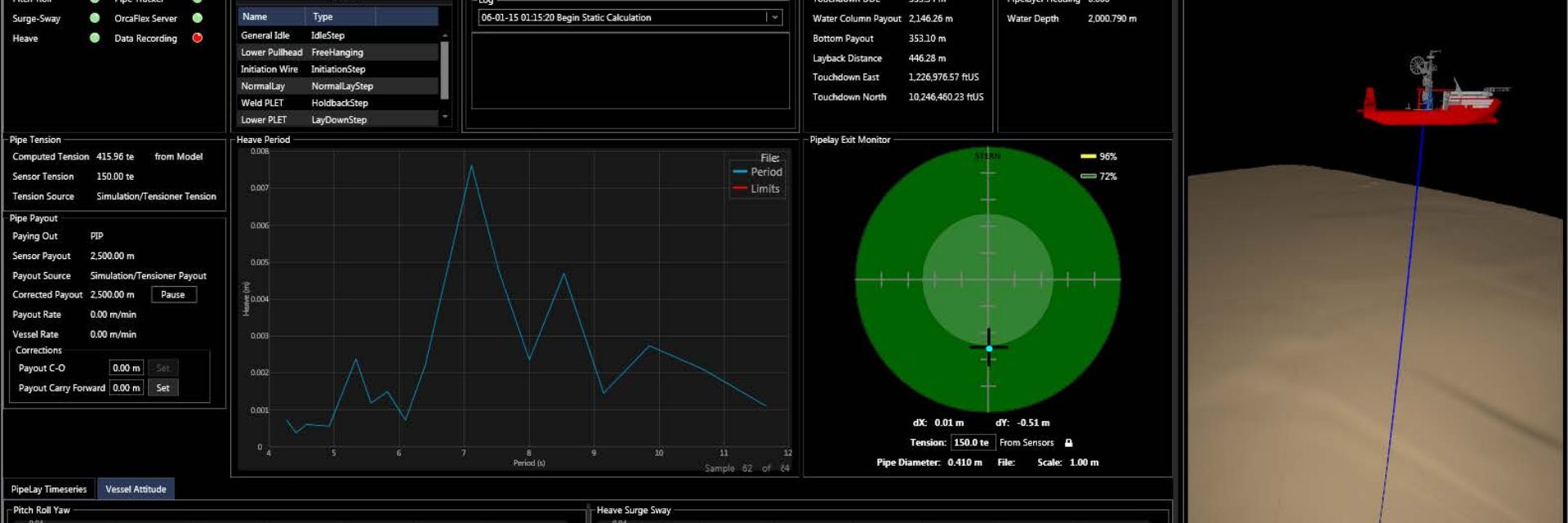
Solutions - Engineering
PipelayView
Real-Time Pipe Installation Modeling
Designed to help pipelay engineers simplify the pipelay installation process, you can leverage numerical and graphical views of pipe installation parameters in real time with PipelayView.
Easily connect to various on-board sensors to obtain vital data and compare it directly with design metrics during installation.
Access Precise Measurements
Rely on PipelayView's optional scanning laser, which can be mounted with a view of the pipe exit from the lay vessel, to gain precise measurement of the pipe exit angle.
You can see the measurements on a bullseye chart that can then be incorporated into your PipelayView screen using 4D Nav's PEMS software module.
Seamless OrcaFlexTM FEA Integration
PipelayView is easily integrated with Orcina's OrcaflexTM FEA (Finite Element Analysis), giving you access to real-time modeling of pipe catenary, touchdown tensions, and fatigue.
PipelayView's Features Include:
- OrcaFlexTM static analysis model
- Continuous vessel position updates
- Measured pipe payout
- Pipe fatigue calculations
- Optional PEMS software module with laser pipe exit angle tracking
- Dynamic exit angle warning zone updates
- Heave amplitude and period calculations with engineering limit comparisons
- Relational database with automated raw data backup and customer deliverables